Slab surface preparation with hand scarf
Scarfing processing has been used widely to remove surface defects from steel and other semi-finished as-cast products for over 70 years. Steel slabs produced from continuous casting often exhibit surface defects, including inclusions, pits and cracks. In order to obtain advanced high strength steels (AHSS) for automotive parts or other high- quality-products, these surface defects should be avoided during the casting process or removed during post-processing using the scarfing technique.
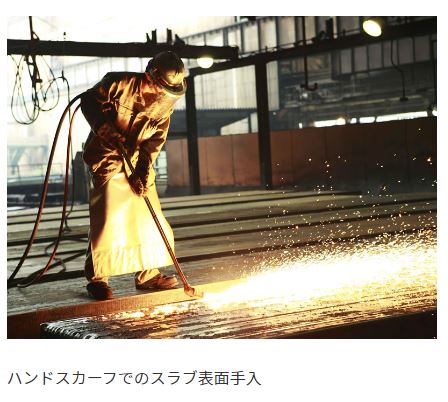
The gas fuel (such as propane C₂Hg) and oxygen leaving the torch combust into a high temperature flame, which heats the slab sufficiently to initiate the exothermic reaction of iron with available excess oxygen to farm iron oxide
(mainly 3Fe+20₂=Fe3O4+972.4 KJ/mol) .
During this scarfing reaction, part of the released heat increases the temperature and melts the iron oxide products (FeO, Fe2O3, Fe3O4) , part of the heat is transported away through radiation and advection with the combustion gas and the rest is conducted into the steel slab. Most of the iron oxides are swept away by the high-speed oxygen and combustion gases as soon as they form, but some of this material remains in liquid slag form which is blown across the surface of the steel slab as an intermittent coating layer. The hot liquid slag coating layer, conducts some heat into the steel slab and provides some preheat for the continuous scarfing reaction process.
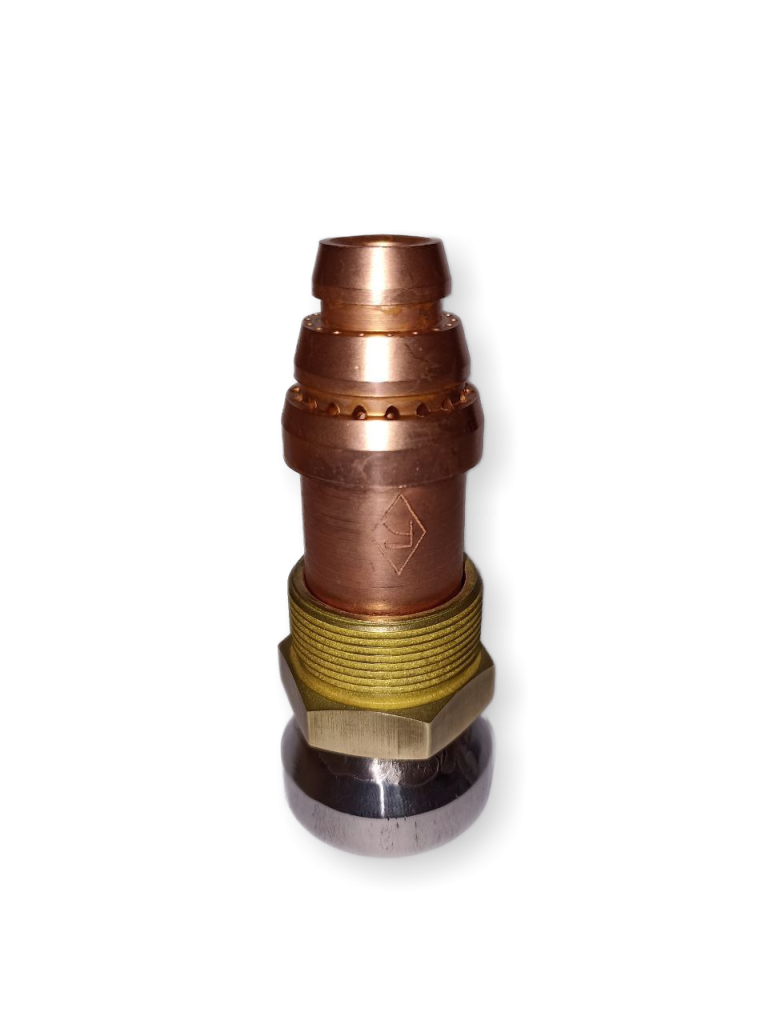
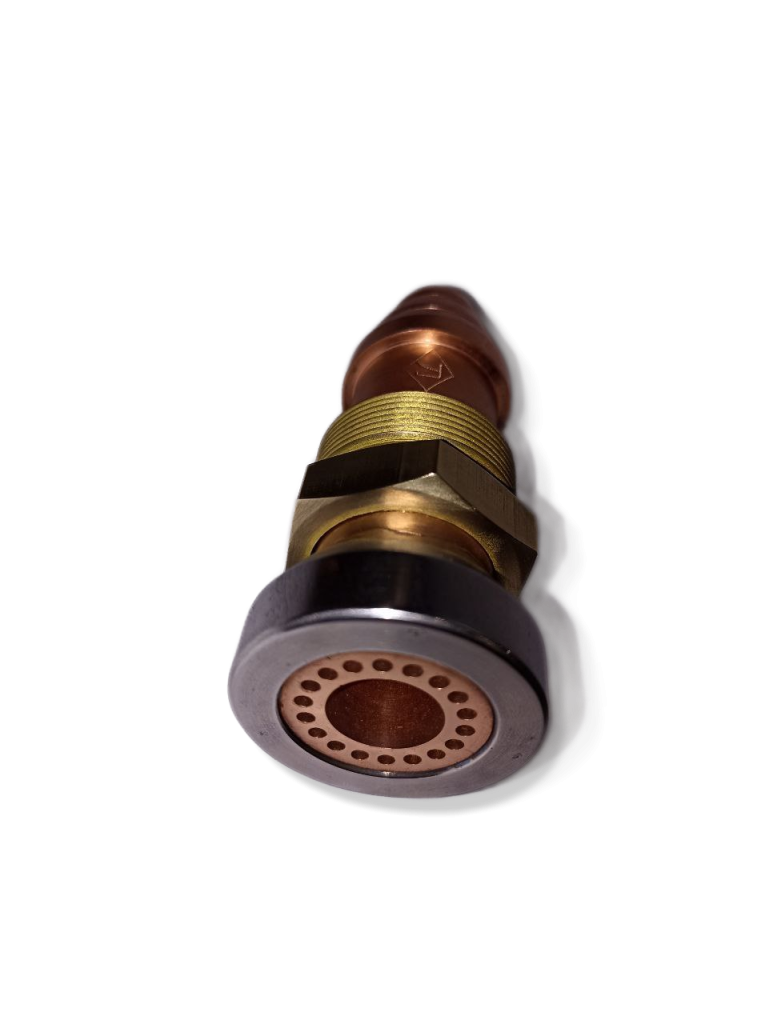
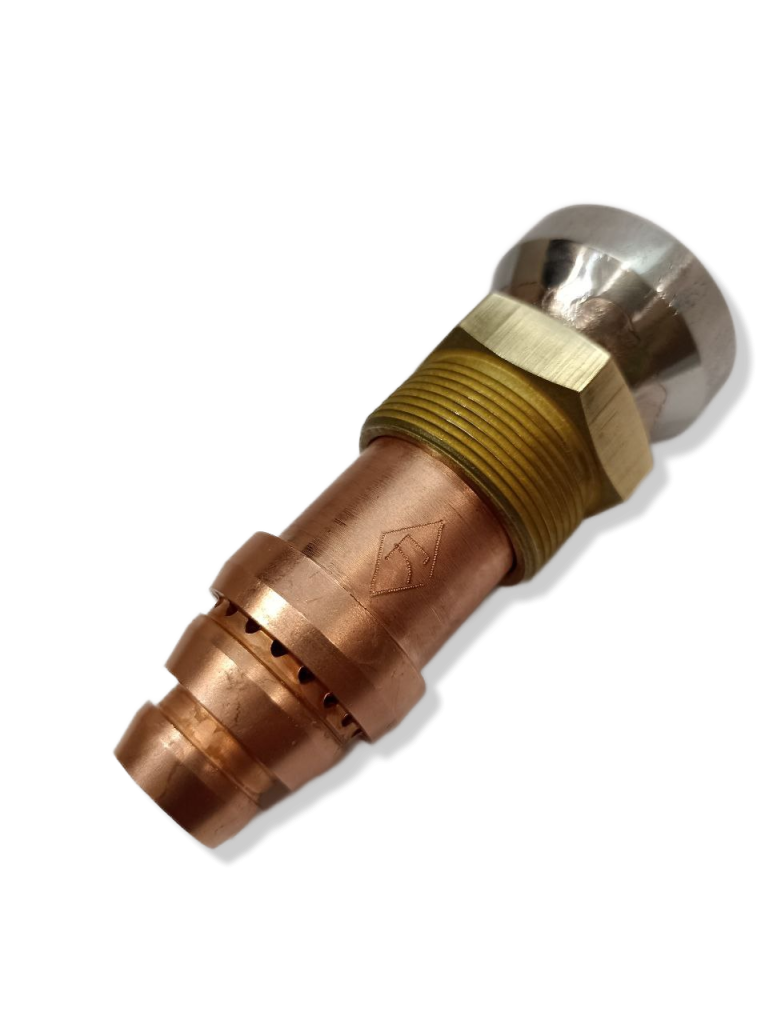
One piece solid copper drilled scarfing nozzle of nozzle mix design. This nozzle produces a wide flat gouge path. This solid copper scarfing nozzle has been fitted with a Stellite wear ring to help prolong the nozzle life. This nozzle is suitable for use every style scarfing torches.
As with all gouging or scarfing nozzles car should be exercised when forward gouging to ensure the dross is being blown forward, try not to allow the molten dross to sit on the nozzle tip face as this will cause the nozzle to burn prematurely.
It is important that the nozzle has sufficient oxygen flow to enable the dross to be blown ahead of the gouge path, high flow equipment has to be used so no restrictions are encountered, scarfing operates best with lower pressures and higher flows – it is the volume of oxygen that is important to the gouge path being achieved correctly plus of course the technique and skill of the artisan.
Should internal burning be encountered then it is important to shut off the oxygen first and then the fuel. If possible quench the nozzle and torch head in clean water then establish why the sustained backfire happened. Inspect the nozzle and torch the refit and test.
Outstanding features:
✔️ Unparalleled Build Quality: This nozzle is made of copper alloy with a Stellite wear end ring, which is designed to withstand high temperatures and pressures.
✔️ Unparalleled Performance: With the optimal internal mix of gases, this nozzle provides you with unparalleled performance in cutting and cleaning metals.
✔️ Stability and Safety: The end ring made of alloy steel of this nozzle provides more safety and stability in thermal and pressure working conditions.
✔️ High lifespan: Using quality materials and advanced manufacturing technology, this nozzle has a longer lifespan.